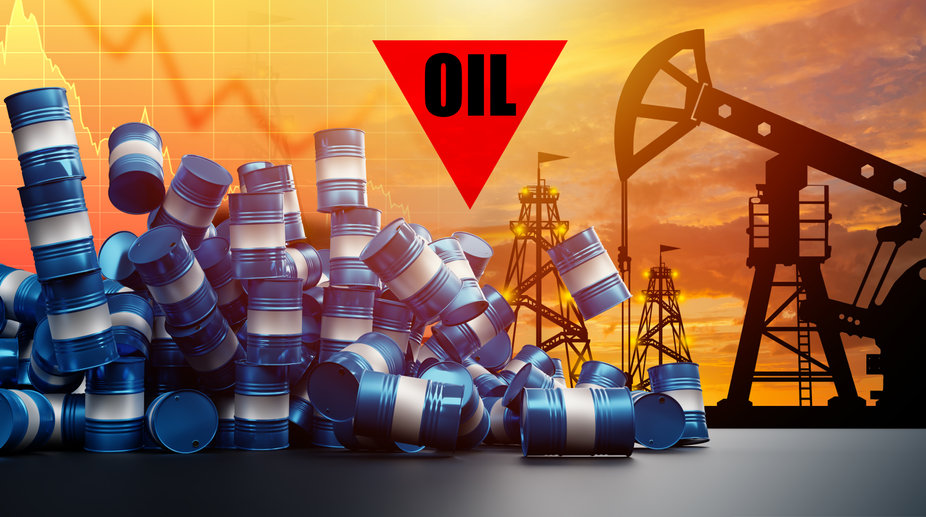
There are numerous manufacturing processes that require the use of a chemical pump. This allows for the safe and easy transfer of harsh substances from tanks, drums, totes, and barrels. These range from modest to complex devices and they are used for pumping a wide array of chemicals. No matter the application, however, it is imperative to ensure that you pick the right chemical drum and this article will cover exactly that.
Pick the Right Pump for Your Application
People tend to associate pumps with chemicals and acids however people don’t realise that pumps can be used for food for example you can get a tomato paste pump. In order to use a chemical drum pump effectively, you need to pick the right one for the application. Here are important elements to consider:
Flow rate- what is the necessary heat and flow for your job? If the application entails unique applications, then you’ll want to pick a chemical drum pump that is designed for higher pressure and flow rates.
Size or portability- do you need to transport pumps throughout the facility? Do you have tight spaces in the facility? For effective use of the pump, ensure you keep any space and portability parameters and needs in mind.
Chemicals- What substances will the chemical pump handle? If you are dealing with toxic or corrosive chemicals, then pick one that is designed to handle those conditions.
Viscosity/gravity– if you intend to pump fluids with high viscosity or gravity ratings, you will need to pick a pump that will handle your specific application.
Temperature- each chemical pump has tubes with temperature limits. As such it is important to consider the maximum temperature of the fluids and pick a pump that can safely handle it.
Pick the Right Accessories
Additional accessories may boost a chemical pump performance or make it ideal for a specific job. That is why manufacturers provide complete lines of accessories in order to make the machinery as effective as possible. Some of the accessories to consider include:
Barrel or Bung Adapters- these come in a wide array of materials and help create a tight tube fit in the barrel. This helps keep the tube in a vertical position.
Filters- this help protect the chemical drum pump from damage by debris and dust.
Nozzles- these allow the operators to gain control of the fluid flow.
Static protection kits- these are used to ascertain safe transfers when combustible or flammable fluids are involved.
Flowmeters- these accessories help the operators precisely measure and control the amount of fluid that’s pumped.
Follow the Right Safety Protocols
Using a chemical drum pump calls for adherence to the right safety standards. To increase production and minimize risk, you will want to follow the following protocols.
Training- anybody who will be installing, running, or maintaining a chemical pump should be properly trained and qualified to do the job.
PPE- before you operate or service a chemical pump, it’s imperative to wear the right personal protective equipment (PPE). This includes gloves, helmets, goggles, face shields, and other gear to protect you from injury.
Power- before running a chemical pump, make sure the power supply is ideal for the motor and that this component is in the off position.
Positioning- always run and store the pump in an upright position.
Cleaning and neutralizing- when pumping are done, or if you intend to change chemicals, it is important to flush the drum pump with clean water or neutralize it with a liquid that’s compatible with the fluids being pumped as well as the pump materials.
And there you have it, vital elements to keep in mind when buying and using a chemical drum pump.